Originally published on fastradius.com on August 2, 2021
Research is an inevitable part of the material selection process — to find out whether or not a particular material is a good fit for your application, you need to do your due diligence. General material descriptions can give you enough information to point you in the right direction, such as whether a particular plastic is suitable for marine applications or if a metal is susceptible to corrosion. To gain an in-depth understanding of a particular material, you’ll need to look at its data sheet.
Material data sheets describe various materials by their properties and are an incredibly useful tool for product teams. However, they can be confusing if you don’t have an engineering or technical background. This article will help you parse material data sheets so you can make informed decisions when it comes to material selection.
Before we dive into the different plastic material properties you can find on a material data sheet, it’s important to understand that reported material sheet properties will depend somewhat on how the material is tested. For this reason, there are usually standards outlining test conditions — like ASTM standards — on a technical data sheet. Here’s everything you need to know.
Tensile properties
Tensile properties, the most commonly reported mechanical material properties, indicate how a material behaves when subjected to pulling loads, forces, and stresses. Some tensile measurements include:
- Ultimate tensile strength — How much stress a material can withstand, beyond which fracture is inevitable. Ultimate tensile strength is usually reported as psi or MPa, which is essentially a force per unit area.
- Tensile strength at yield, or yield strength — How much stress a material can take before irreparable, permanent deformation. Yield strength is usually reported as psi or MPa.
- Tensile elongation at yield — How much a material can stretch before irreparable deformation (“stretchiness”). Tensile elongation at yield is usually reported as a percentage increase in length.
- Modulus of elasticity — How much a material deforms under stress (“stiffness”). Modulus of elasticity is usually reported as psi or MPa.
It’s common to use tension via tensile tests to determine a material’s mechanical properties. Tensile tests are designed to discover how strong a material is, how stiff it is, and how much it can elongate or stretch. The test is simple — one of the clamps pulls on the material until it breaks.
The force applied is measured during a tensile test, then divided by the cross-sectional area of the test sample in order to measure “stress.” Change in length, or “strain”, is also measured. Stress and strain are then plotted in order to understand the relationship between them, from which many mechanical properties can be determined.
Flexural properties
Flexural properties, another commonly reported type of mechanical material properties, indicate how a material behaves when subjected to bending loads, forces, and stress. While some objects require increased flexural properties for use in structural supports, other components need more flexibility in order to avoid damage. There are two particular flexural properties you’ll usually find on a technical data sheet:
- Flexural strength — How much stress a material can take before permanently bending
- Flexural modulus — The tendency of a material to resist bending, represented by a stress to strain ratio
Usually, a three-point flexural strength test is used to determine flexural strength and flexural modulus. This involves placing a bar of the material across two supports, then applying pressure to the center of the bar with a hydraulic head press. It’s common for a material’s flexural strength to be higher than its tensile strength. Filled or reinforced polymers, like polyamides and acetals, boast increased flexural properties, whereas flexible materials such as elastomers usually have lower flexural strength and modulus.
Impact properties
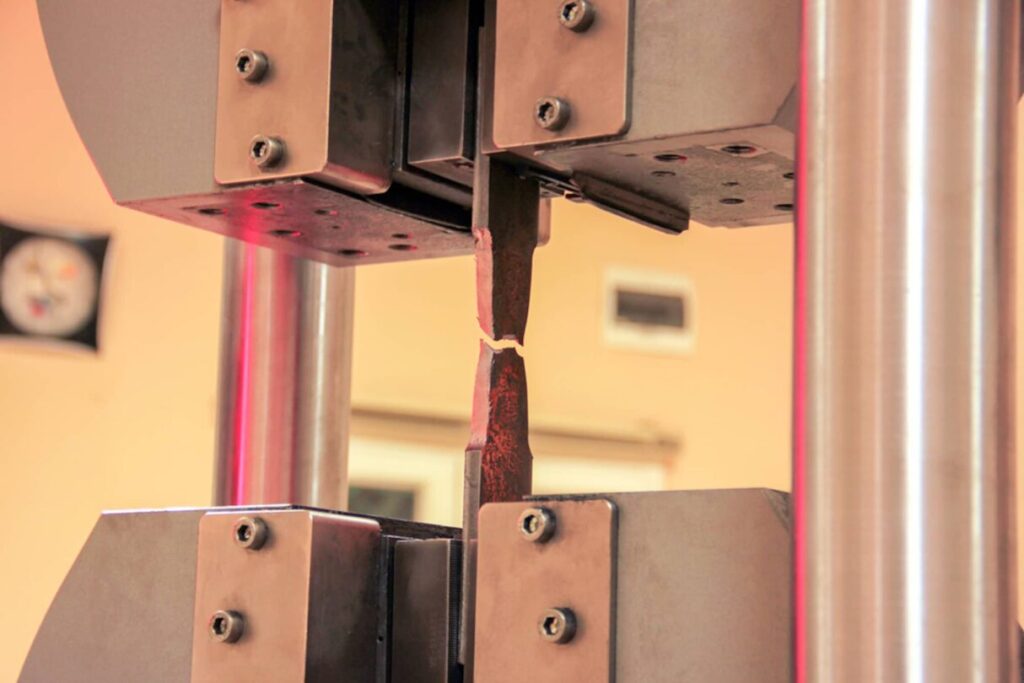
Impact properties refer to how much impact a material can withstand, which essentially means how much energy it can absorb without breaking. The most common way to test for impact properties in North America is using the IZOD impact testing system. To test for impact strength, a material sample is secured in a clamp. A heavy pendulum arm is raised, then swings down and impacts the material sample.
There are two kinds of impact strength testing — notched tests and unnotched tests. Notched impact testing involves hitting the arm against a notched surface, whereas in unnotched tests the arm swings onto a flat surface. Notched tests tend to give more realistic results and are therefore more popular than unnotched tests.
A material’s individual qualities influence its impact properties. Generally speaking, rubbery materials yield better impact resistance because of their high elongation at break. Long-chain branches and greater crystalline structures can also increase a plastic’s impact properties.
Hardness
The hardness of a material determines how well it can resist deformation caused by localized abrasion or indentation. Since the range of hardness is enormous, covering super soft to incredibly hard materials, there are various scales used to measure and determine material hardness. The two most common material hardness scales are:
- Rockwell scale, used for measuring hard materials like metals or gemstones.
- Shore scale, which is used to measure the hardness of polymers. Shore scale can measure softer materials, like gels and rubbers, as well as more rigid materials such as nylon and polypropylene.
During a hardness test, a small ball-ended or cone-ended rod presses into a material sample at a specific force, and how much the rod presses into the material determines its hardness.
Thermal properties
A material’s thermal properties indicate how it reacts to temperature. Here are the core thermal properties of a material:
- Continuous Service Temperature — Indicates the temperature above which mechanical properties are greatly decreased
- Heat Deflection Temperature — Measures the stiffness of a material as temperatures increase
- Coefficient of Linear Thermal Expansion (CLTE) — Describes the propensity of a material to change size due to a change in temperature
- Thermal conductivity — Describes how much a material increases in temperature with respect to the amount of energy subjected to it
Testing for thermal properties is straightforward, except when it comes to determining a material’s glass transition temperature. Only amorphous materials that don’t have crystalline structures, like polycarbonate and polystyrene, have a glass transition temperature. This, measured in Tg, determines the heat at which a material becomes rubbery.
Material data sheet decoding with SyBridge Technologies
Reading a material data sheet is an excellent way to start learning more about prospective materials for an upcoming project. However, as you can see in this article, a technical data sheet can be challenging to understand. Plus, it’s no substitute for expert advice.
An experienced manufacturing partner like SyBridge Technologies can help guide you through the material selection process and demystify complex material data sheets. SyBridge Technologies team members have vast industry knowledge and experience, and we’ll use that expertise to ensure you’re choosing the right material for your application. If you’re ready to start your next project, contact us today.