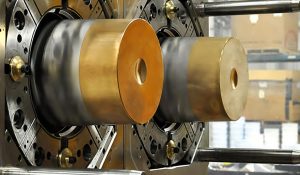
Optimizing Your Injection Molding Process for Cost-Effective Manufacturing Excellence
In today’s competitive landscape, manufacturers are constantly seeking ways to streamline their processes, reduce costs, and increase output. At SyBridge, we understand these challenges and are dedicated to partnering with you to achieve your manufacturing goals.
Our expertise in design, engineering, and tooling for injection molding goes beyond simply creating high-quality molds. We are your strategic partner, offering expert guidance to optimize your entire process, resulting in measurable improvements to your bottom line.
Case Study
Optimizing a Pail Mold for Increased Efficiency and Cost Saving
A recent collaboration with a client perfectly exemplifies the value SyBridge brings to the table. We were tasked with re-engineering an existing pail mold. The original design presented several challenges, including:
- Average cycle times: The initial cycle time was 20 seconds, limiting overall production output.
- Limited output: The mold could produce 1 million parts per year; however, growing demand required additional output.
SyBridge’s Expertise Delivers Remarkable Results:
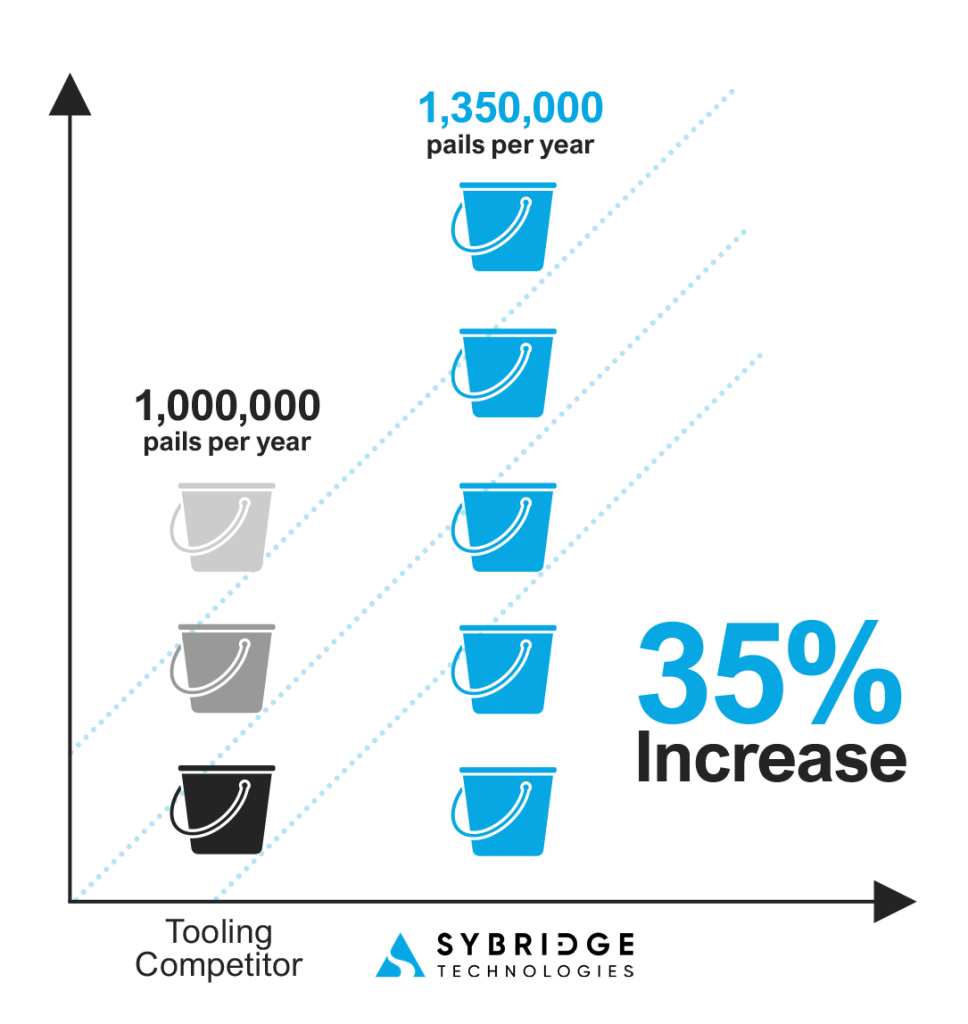
Our team of engineers meticulously analyzed the existing mold and identified optimization opportunities. By leveraging our expertise in precision tooling and complex high-cavitation tools, we were able to:
- Reduce cycle time by 15% (3 seconds):
This seemingly small improvement translates to significant production volume increase over time. - Increase output by over 30%:
The new design allows for the production of 1,350,000 parts per year, exceeding the client’s initial requirements. - Consolidate production:
The optimized mold’s increased efficiency enabled the client to manufacture at the same rate as four presses while using only three, eliminating the need for additional equipment and tooling costs.
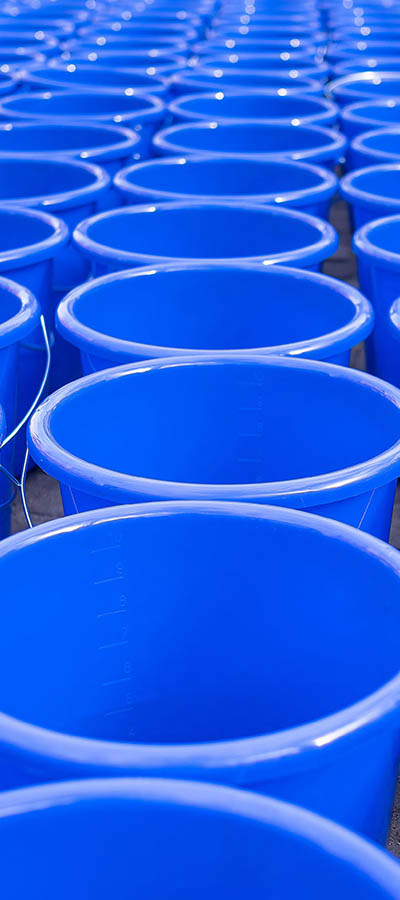
The Impact
Measurable Cost Savings and Increased Profitability
These improvements translate into tangible financial benefits for our client. They were able to:
- Avoid the significant expense of purchasing and integrating a new injection molding press.
- Eliminate the cost of additional tooling required for a four-press operation.
- Realize increased production capacity to meet growing demand and potentially capture new market opportunities.
Beyond Efficiency
Maintaining Product Integrity
It’s important to note that these improvements were achieved while maintaining the product’s critical performance requirements. The new mold design successfully met all drop testing, shipping testing, and leak testing specifications, ensuring product integrity without compromising efficiency.
SyBridge
Your Partner for Optimal Injection Molding Solutions
This case study is just one example of how SyBridge’s expertise can help manufacturers optimize their injection molding processes and achieve significant cost savings, increased output, and improved profitability. Our commitment to precision engineering, innovative solutions, and collaborative partnerships makes us your ideal partner for navigating the ever-evolving landscape of injection molding.