Originally published on fastradius.com on August 7, 2020
The boom of commercial 3D printing has given rise to a number of common misconceptions about the process. For instance, many believe that additive manufacturing processes can only use plastics. In reality, engineers can also create 3D printed parts using metals.
For projects involving metals, engineers should familiarize themselves with the advantages and disadvantages of both metal injection molding (MIM) and metal 3D printing. A closer look at the two processes shows that metal 3D printing offers a surprising range of benefits. Here are the key differences — plus key considerations — for engineers.
Metal injection molding (MIM)
Metal injection molding (MIM) combines plastic injection molding with powder metallurgy and requires four stages — feedstock preparation, molding, debinding, and sintering.
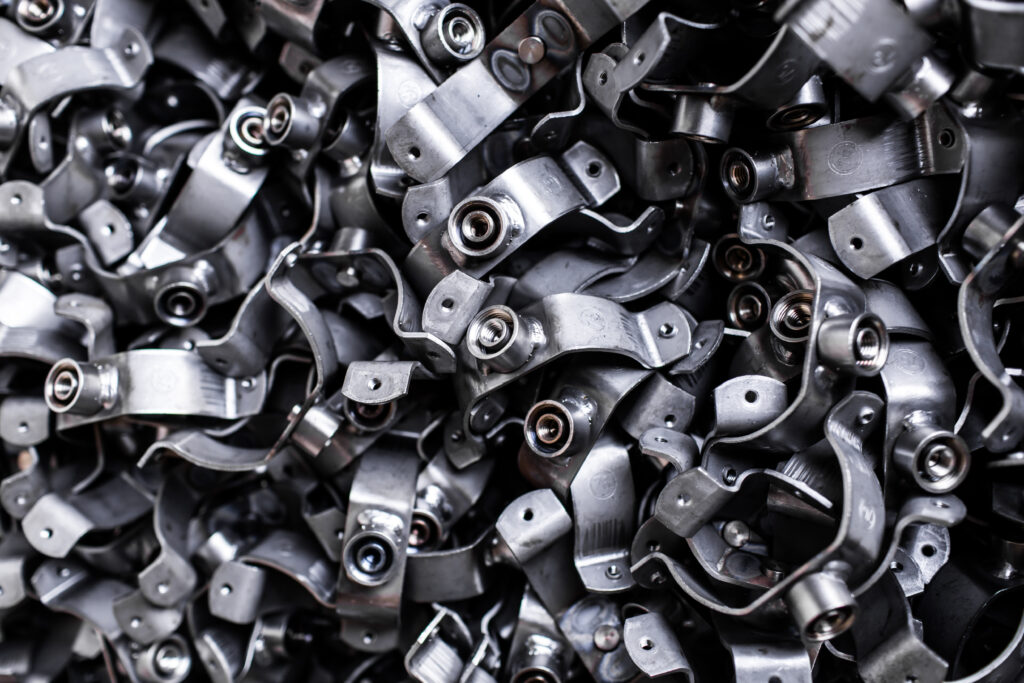
First, fine metal powders are combined with thermoplastic material and wax binders and then granulated into small pellets. These pellets are then heated and injected into a mold cavity. After molding, the binder is removed from the metal powder, resulting in a “brown part,” which moves onto the sintering stage. The furnace cycle typically involves a number of stages. The brown part is heated to a relatively low temperature to burn out any remaining binder, then it is sintered at a temperature near the melting point of the metal. The metal powder densifies to produce the final product.
Applications
Engineers turn to MIM when they need to produce parts — particularly small or complex ones — that cannot be efficiently manufactured with any other process. Since only one mold is required to make a part with MIM, this process is also highly repeatable and yields parts that are uniform in size, shape, and strength.
MIM parts have a wide range of applications in major commercial and industrial sectors, from automotive to aerospace. Common applications include hinges on eyeglasses components, watch cases, laptop hinges, and precision medical instruments.
Benefits
MIM is an efficient method by which to produce a high volume of small, complex parts. Finished parts have a smooth surface finish and are relatively strong for their size, often yielding above 95% density. MIM is compatible with a wide variety of materials that can be broken down into a powder form and are suitable for sintering. These are mostly steels.
Limitations
Unfortunately, metal injection molding comes with numerous limitations, primarily due to the molds required to produce MIM parts. MIM molds can cost anywhere from $50,000 to $100,000, which could be prohibitively expensive for low-volume production runs. Often, MIM makes financial sense for annual volumes over 50 thousand with a long production lifecycle.
Further, metal injection molding poses considerable design challenges for engineers. Mold designs aren’t easily changed and there are still significant limitations in regard to shape. For instance, the part cannot have large overhangs, as it has to be ejected out of the cavity. Wall thickness presents another design challenge due to debinding. If the part walls are too thick, it may be impossible to extract the wax from the middle. Designers and project managers must keep these considerations in mind if they plan to use metal injection molding for their project. If not, they might be forced to make costly adjustments later on in the manufacturing process.
Metal 3D printing
Metal 3D printing offers many advantages that other processes, including MIM, cannot match. One kind of metal 3D printing is laser-powder bed fusion (L-PBF), sometimes known as DMLS, which is a printing process that produces parts from metal powder.
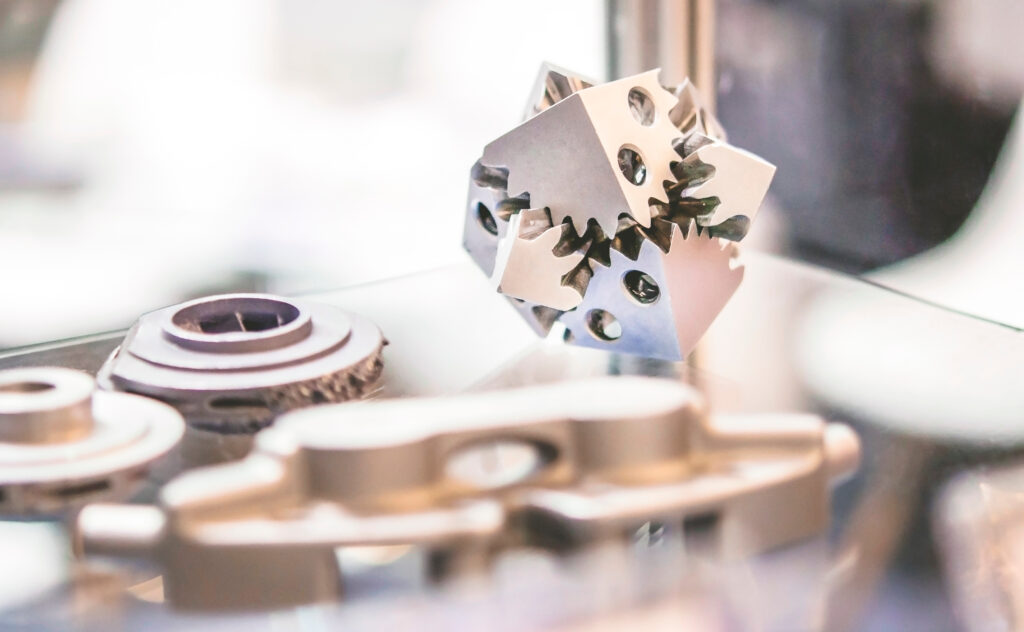
During this process, a chamber is prepped with an inert gas like argon to minimize oxidation. A thin layer of metal powder is spread on the top of the build platform and then a laser melts the powder together in small sections; the process repeats until the part is fully built. Excess powder is removed after the part cools. From there, the part is stress-relieved, detached from the build plate, and then heat-treated if necessary.
Applications
Parts made from the L-PBF process are ideal for industrial applications and high-performance end-use engineering parts. Common use cases include jet engines, turbine blades, medical equipment, and power generators. This process is compatible with a growing list of metal alloys and even some precious metals like gold and platinum. There are also other metal 3D printing processes that are better suited for applications with fewer regulation and critical performance requirements, such as metal binder jetting and metal extrusion.
Benefits
Engineers turn to metal 3D printing when they need to create specialized parts that require high strength and durability, chemical resistance, and access to unique design features. Unlike metal injection molding, metal 3D printing offers engineers a great amount of design freedom. Metal 3D printing does not use molds, so engineers are not beholden to certain shape limitations, and changing the design of a part is as simple as updating the design on a computer. Making a design more complex won’t contribute to additional production costs.
Limitations
That said, metal 3D printing does have its own set of challenges. Build size is limited due to the strict manufacturing conditions and process controls required. Also, metal 3D printing startup costs for an industrial-grade machine can soar into the millions — before factoring in the cost of materials. However, the high price tag can be a worthy investment for engineers who want unmatched design flexibility and great mechanical strength.
Get started with metal 3D printing
Metal injection molding is well-suited for creating small, complex parts that are surprisingly strong for their size. However, metal 3D printing outpaces this process in many key areas. Metal 3D printing offers more design versatility and parts made with this process can be optimized for high strength, durability, and chemical resistance.
At SyBridge, we’re well-versed in additive manufacturing with a variety of different materials. Whether your parts require plastic or metal, our team of experts will help you get started and guide you every step of the way. It’s never too early to start working toward your vision — contact us today.