Forget typical cycle times. We’re pushing the boundaries of conformal cooling. While traditional approaches deliver reductions, at SyBridge, we see further. By combining our expertise in 3D printing, mold tooling design, and in-house manufacturing, we engineer conformal cooling solutions that unlock the true potential of this transformative technology. Our unique synergy allows us to not just achieve impressive results, but to truly test the limits of what conformal cooling can accomplish for your product.
Conformal cooling improves throughput
SyBridge uses conformal cooling designs–either in retrofitting older tooling or as an initial design element–to enhance cooling efficiency, reduce cycle times, and increase productivity (Figure 1).
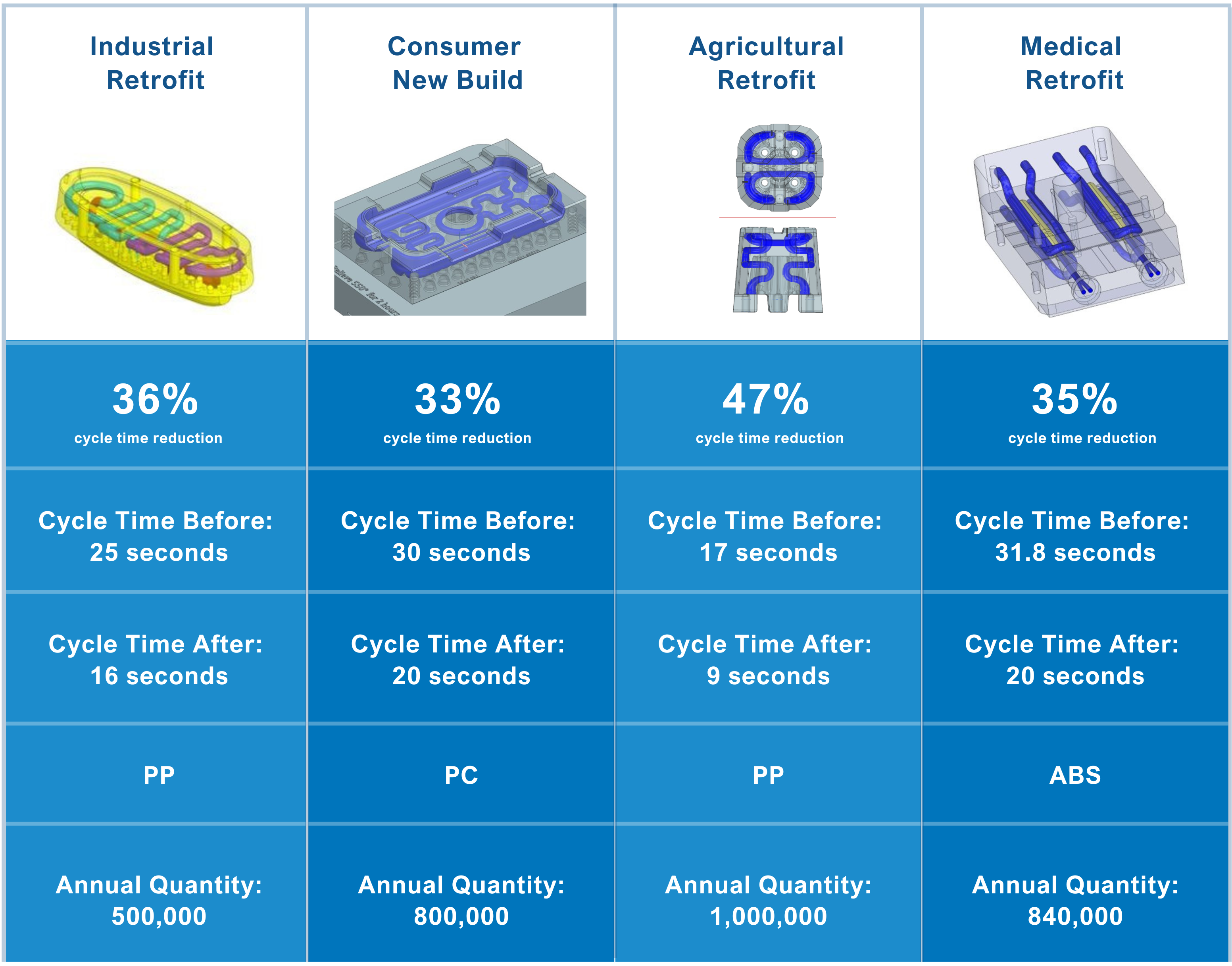
In one redesign, after a mold flow simulation revealed hot spots on the tips of the parts, SyBridge experts engineered precision water channels to enhance cooling efficiency. Their unique design focused on cooling the front tip of the part, which enhanced the cooling of the rest of the part. This design change substantially reduced mold-open time. Figure 2 dives deeper into the results of these conformal cooling design enhancements.
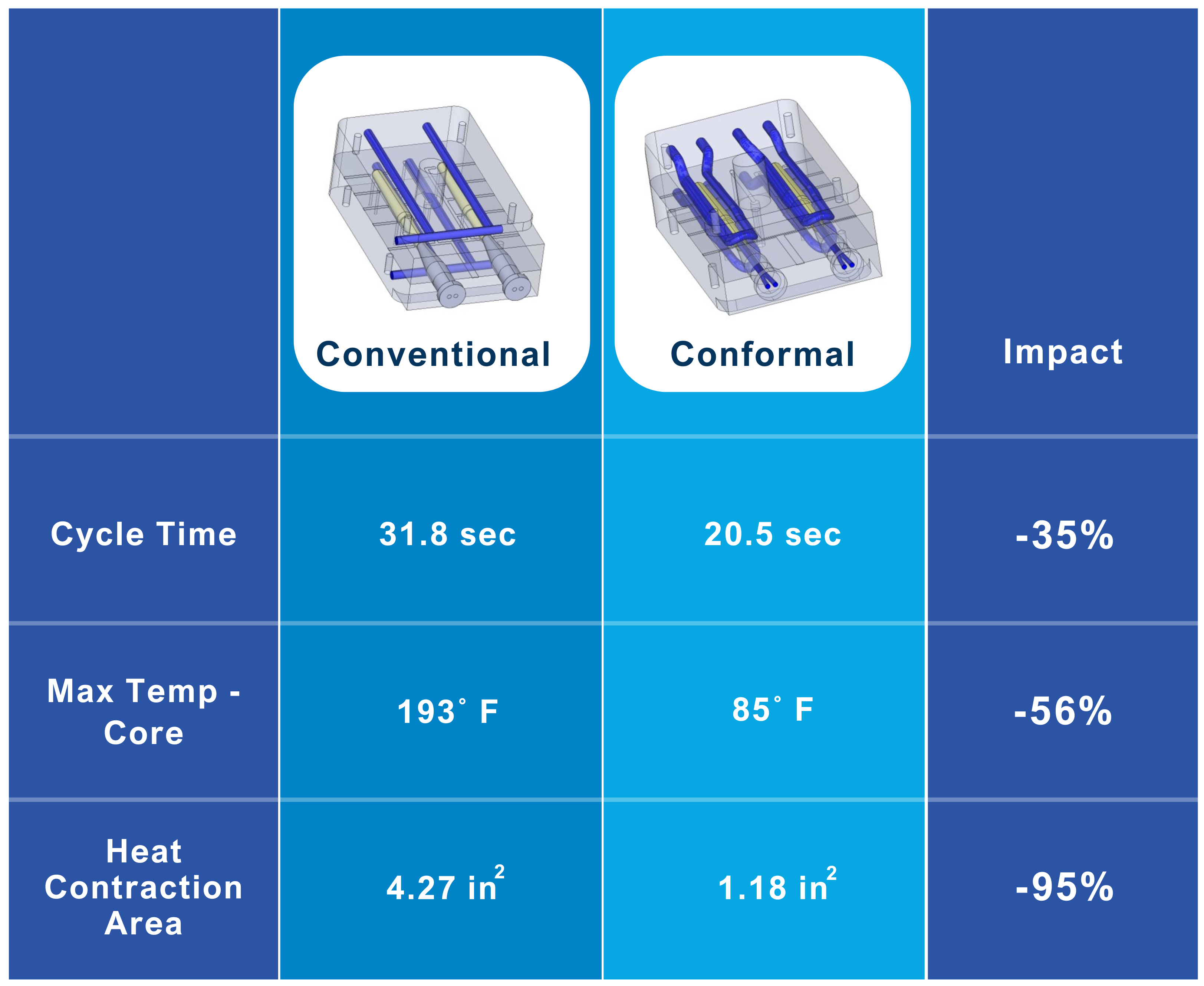
It takes experience to design effective conformal cooling
Additive manufacturing (AM or 3D printing) is an excellent avenue for designing conformal cooling. AM enables intricate and complex structures that closely conform to every shape of the part in a way that–depending on the part geometry and complexity–is not always possible with subtractive manufacturing. During the design phase, long before the part is molded, SyBridge engineers use mold flow simulation, virtual testing, and digital integration to configure and test the conformal cooling capacities.
Can we help you reduce cycle times?
As conformal cooling experts, SyBridge engineers know how to help you get the cycle times and efficiencies your product needs. Contact our team to explore how solutions like conformal cooling can improve your injection molding process.