Originally published on fastradius.com on June 14, 2021
A thread is a small ridge wrapped around the length of a cylinder in a spiral shape. They’re used to either convert rotary motion into linear motion or prevent linear motion without the corresponding rotation. Internal threads, like the standard nut, are threads found on the inside or concave surface of a part, while external threads — screws, bolts, and studs — are threads found on the outside of the part.
Internal and external threads can be found in products made using a variety of manufacturing processes like injection molding and 3D printing, but they’re most commonly produced via CNC machining. It’s much easier to add threads to milled and turned parts. To add industrial threaded products to a CNC machined part, engineers and product teams should keep a few factors in mind during the design phase.
When Should You Use Threads?
It’s much easier to thread parts where the hole is perpendicular to the surface through which it runs. If your tapping tool is perpendicular to the surface of the part, it can fully engage on that first turn, whereas the tapping tool can have difficulty grabbing onto the surface if you’re at an obtuse or acute angle.
There aren’t many placement restrictions when it comes to threads. As long as the thread is placed somewhere that’s accessible to the CNC turning or CNC milling tool, you can trust that it’s in the right place. Also, it’s best to use standard hole and thread sizes. However, there are other factors to consider when it comes to screw design.
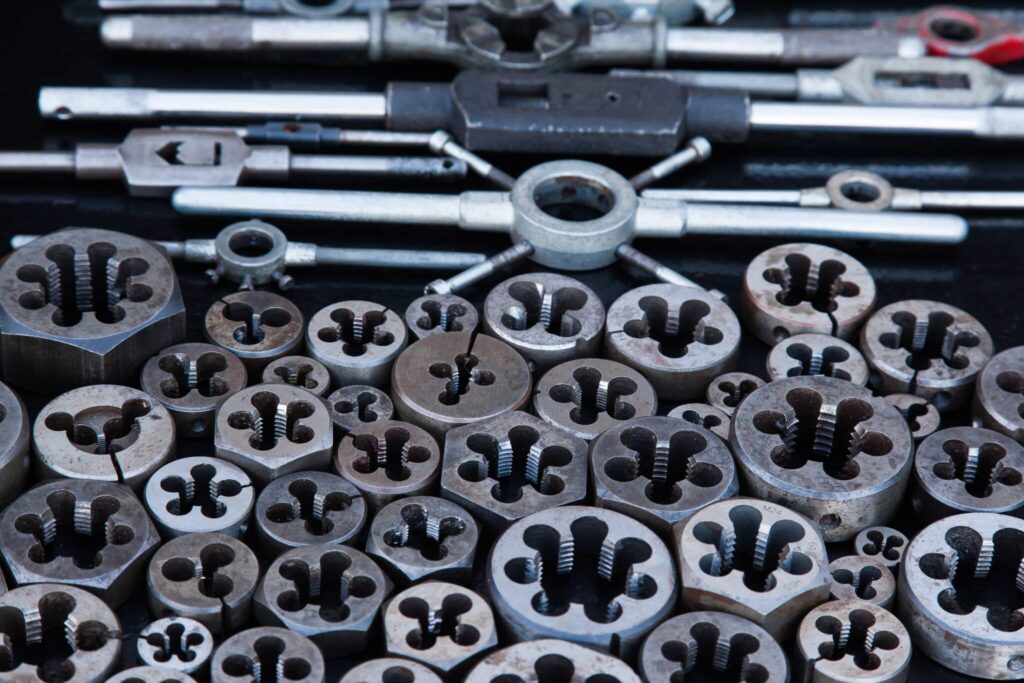
Internal and External Thread Design Tips
Depth and diameter are important considerations for designing industrial threaded products. For instance, long thread sections are rarely necessary. Since most of a part’s stress is placed on the first three threads, having more threads isn’t beneficial beyond a certain point.
It’s also important to pay attention to the various diameters involved in thread design, like the major thread, minor thread, and the diameter of the pilot hole. If you have a pilot hole that has the same diameter as the major thread of the mating screw, the mating hardware will not engage with the hole.
To avoid pain points like these, ensure that any thread’s pilot hole allows for appropriate tap engagement. Most CAM programs have features that will be able to help you determine the right measurement.
Here are some other tips and tricks for designing internal threads:
- Include a countersink at the end of internal threads.
- Reduce the number of threads whenever possible.
- Use standard thread forms and sizes to cut down on production costs.
- Keep in mind that coarse threads tend to be more cost-effective than fine threads.
- Whenever possible, make the surface of the starting end of the thread flat and consistent with the central axis of the thread.
External threads are a little more forgiving. To design superior threaded products, include a chamfer in all screw designs and do your best not to terminate near the shoulder of areas with large diameters. Just like internal threads, it’s best to use shorter external threads unless the CNC machined part needs high thread strength.
Design Superior Threaded Products With SyBridge
Internal and external threads may be small, but they play an essential role in product development. They connect screws to other components and help engineers and product teams design for manufacturability. To design superior threaded products for CNC machining, it helps to tap into expert advice.
A seasoned manufacturing partner like SyBridge can help you perfect your threaded part designs and optimize CNC machined parts. Our team of designers, machinists, engineers, and technologists have access to the latest digital design technologies and come to the table with years of CNC machining service experience.
SyBridge has in-house CNC machining capabilities — so you can trust that your parts, and industrial threaded products, will be manufactured according to the highest quality standards and delivered on-time and within budget. Contact us today to get started.