Originally published on fastradius.com on March 16, 2022
3D printing is an innovative and versatile manufacturing method capable of producing many different kinds of complex parts, but many 3D printed parts have coarse surface finishes with tiny gaps after the initial printing. Parts produced using fused deposition modeling (FDM), for example, often have prominent layer lines before post-processing.
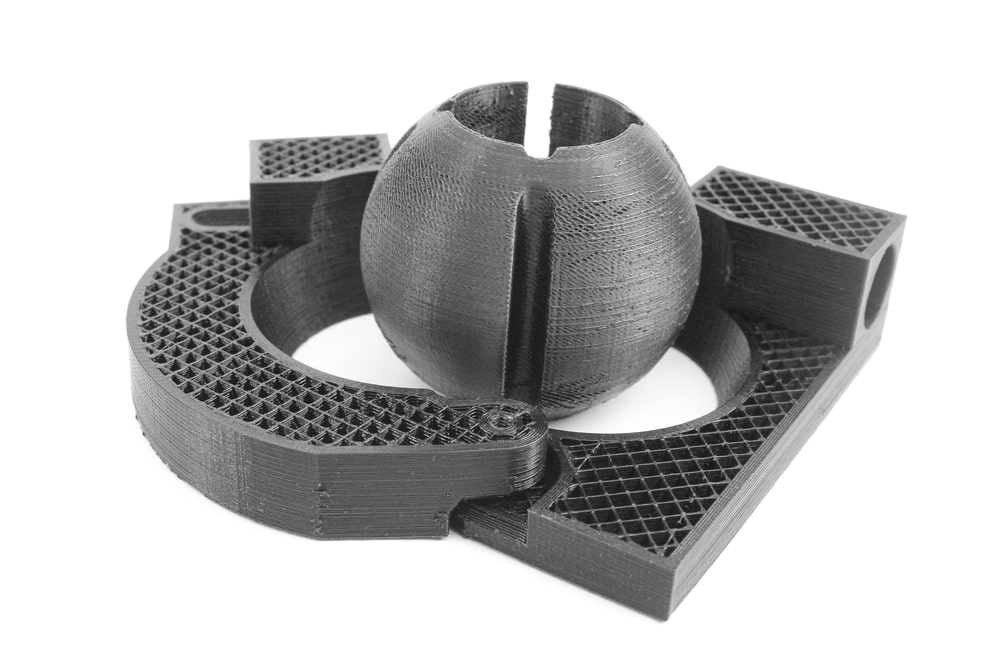
To smooth out the surface of a 3D printed part, engineers apply coatings, use abrasive media tumbling or sanding, finish the part by hand, or use a technique called vapor smoothing. Here’s everything you need to know about using vapor smoothing to improve your part’s cosmetic appearance and enhance its mechanical performance.
What is Vapor Smoothing?
Vapor smoothing, also known as chemical vapor smoothing, is a post-processing option that involves exposing printed parts to vaporized solvent. Vapor smoothing your parts eliminates sugar cube-like finishes or layer lines and replaces them with smooth, glossy surfaces. In addition to refining a part’s cosmetic appearance, vapor smoothing 3D prints can help you boost their mechanical performance without sacrificing your part’s features, ultimate tensile strength, or dimensional accuracy.
Vapor smoothing is compatible with most 3D printed polymers and elastomers. Common materials include:
- Acrylonitrile styrene acrylate (ASA)
- Acrylonitrile butadiene styrene (ABS)
- High-impact polystyrene (HIPS)
- Nylon 11 (PA 11) and Nylon 12 (PA 12)
- Polypropylene (PP)
- Polycarbonate/acrylonitrile butadiene styrene (PC-ABS)
- Polyethylene terephthalate glycol (PETG)
- Polylactic acid (PLA)
How Vapor Smoothing Works
To achieve high-quality, easily repeatable results, vapor smoothing is best performed in a controlled environment with industrial-grade 3D printing vapor smoothing equipment.
If you work with an experienced manufacturing partner, their engineers will carefully hang your parts in a sealed process chamber to maximize their exposure to the vapor. Then, they’ll introduce dissolvent fumes to create a controlled chemical melt that liquefies and redistributes material, which evens out surfaces, seals tiny cavities, and enhances shine.
Finally, they’ll heat the chamber and evacuate the vapors into a collection vat before the vapors can round out your part’s surfaces. Your final part will be watertight and have smooth internal cavities, accurate dimensions, and the same amount of material as before smoothing. Also, vapor smoothing won’t negatively affect your part’s mechanical properties. In some cases, it can even improve them.
When designing parts that will be vapor smoothed post-printing, you’ll want to keep your wall thicknesses uniform and add radii to any sharp internal corners to prevent rounded voids. Keep in mind that flexible materials are more likely to have surface imperfections than rigid ones. Also, getting the timing right is essential when vapor smoothing moving parts or any pieces with joints, as exposing them to vapors for too long can reduce joint integrity or melt pieces into one another, causing sticking.
It’s also important to note that vapor smoothing isn’t the best solution for every print. Models that are too complex, small, large, or flat may deform or lose detail, and rack marks may be visible afterwards.
The Benefits of Vapor Smoothing
Vapor smoothing allows you to achieve smooth and watertight surface finishes comparable to those of injection molded parts without significantly increasing lead times. Vapor smoothing can also enhance a 3D printed part’s color consistency and hue; significantly reduce moisture absorption; and boost elongation, tensile, and flexural performance — all while retaining its features, ultimate tensile strength, and dimensional accuracy.
Vapor smoothed parts are also safe for skin and food contact, and they pass cytotoxicity and microbiological bacteria health and safety tests. Vapor smoothing polishes non-line-of-sight features without leaving any residual chemicals or media behind and, since it takes place in a carefully controlled environment, you can repeatedly achieve the same results.
Since vapor smoothed parts are watertight, experience less bacteria growth, and don’t have any residual chemicals, the medical and automotive industries often use vapor smoothing to finish 3D-printed parts. Companies can use vapor smoothing for everything from concept models to prototypes to final products.
Smoothing Printed Parts With SyBridge
Vapor smoothing has lots to offer — from improved part aesthetics to easier cleaning to increased safety. However, you’ll need industrial-grade vapor smoothing equipment and the help of a professional manufacturer to achieve the best results.
When you work with SyBridge, our team of experts can guide you through the entire production process, including the complicated decision of what post-processing method is best for your part and application. Contact us today to learn more.