Previously published on fastradius.com on September 28, 2020
Stereolithography (SLA) is an additive manufacturing process that uses photopolymerization to build plastic parts with complex geometries, fine details, and smooth surface finishes. This process is applicable to a wide variety of industries thanks to the wide variety of SLA-compatible resins on the market today. For example, dental and surgical-grade resins satisfy all biocompatibility requirements in the medical industry, and heat-resistant resins can be used for casting and thermoforming tooling.
Product teams turn to engineering-grade, or “SLA tough” resins when they want to mimic the look and feel of acrylonitrile butadiene styrene (ABS) plastics and manufacture parts with superior mechanical and chemical properties. Here’s a comprehensive breakdown of SLA tough resins, plus a few top SLA tough resin brands that product teams should consider using.
SLA Tough Resin Applications
SLA tough resins were designed for applications requiring materials that could withstand high stress or strain for short periods of time. As such, these resins are extremely stiff, resistant to cyclic loads, and very strong. Common applications include sturdy, shatter-resistant parts like enclosures or seat belt clasps and high-performance 3D prototypes. SLA tough resins are also ideal for wearable technologies, gadgets, and other small products that must withstand a fair amount of wear and tear.
SLA Tough Resin Disadvantages
SLA tough resins do have a few drawbacks. For instance, these resins typically have a low heat deflection temperature and are relatively brittle compared to other plastics. Beyond that, SLA resins can limit product teams in terms of design. They’re ill-suited for parts with thin walls and finished parts may be difficult to remove from the build platform.
Why Use SLA Tough Resin?
Limitations notwithstanding, there are many reasons why product teams would opt for SLA tough resins over standard resins. Standard photopolymer resins used for SLA are generally very fragile, and the finer details of a part are prone to snapping or cracking under pressure. As such, standard resins are typically used for projects where aesthetics are more important than performance.
Engineers don’t have to sacrifice strength for style with SLA tough resins. With this material, engineers can build durable, high-resolution parts without worrying about constant breakage. SLA tough resins strike the right balance between strength and compliance.
For optimal results, follow these best practices for printing parts with SLA tough resins:
- Avoid printing directly on the build platform — instead, employ supports and warm the platform with heated air to ease removal.
- Wash the finished parts in isopropyl alcohol for 20 minutes maximum.
- Increase flexural stiffness and flexural strength with post-curing.
Three Top SLA Tough Resins
There are many SLA tough resins on the market for engineers to choose from, but these three brands are widely considered the best of the best.
1. Formlabs Tough Resin
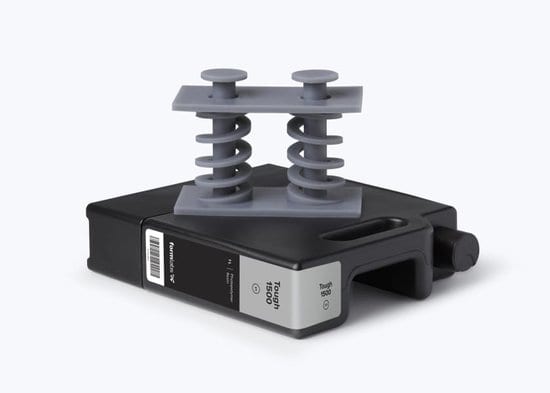
Formlabs Tough Resin can outpace materials like ABS when it comes to elongation, impact resistance, and yield strength. This resin’s high strength comes from its chemical formulation — it’s made from the strongest materials in Formlabs’ line of Tough and Durable resins and doesn’t have any additives. This material is ideal for sturdy prototypes, functional parts, and assemblies that will undergo brief periods of stress. The technical specifications for Formlabs Tough Resin, post-curing, include the following:
- Tensile strength: 55.7 MPa
- Flexural strength (at 5% strain): 60.6 MPa
- Flexural modulus: 1.6 GPa
- Elongation at break: 24%
- Notched IZOD impact strength: 38 J/m
2. eSun Hard-Tough Resin
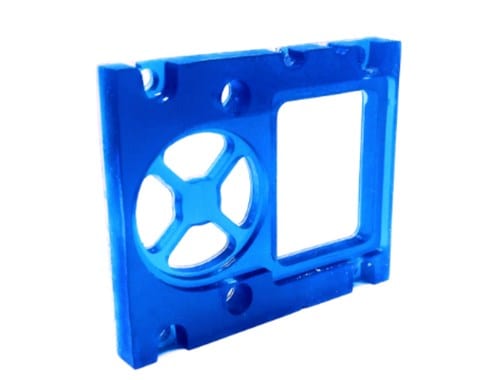
eSun Hard-Tough Resin is well-known for its toughness, hardness, and high physical strength. This resin is ideal for high-performance applications and building parts that must withstand high-impact forces and other mechanical pressures.
For best results, eSun engineers recommend printing at an operating temperature between 18-35°C. The best wavelength is between 395 and 405 nm, and the recommended exposure time is eight seconds for a normal layer and 20-30 seconds for a bottom layer. The technical specifications for this resin, post-curing, include:
- Tensile strength: 50-60 MPa
- Flexural strength: 70-80 MPa
- Flexural modulus: 1300-1400 MPa
- Elongation at break: 30-50%
- Notched IZOD impact strength: 67-100 J/m
3. Liqcreate Strong-X
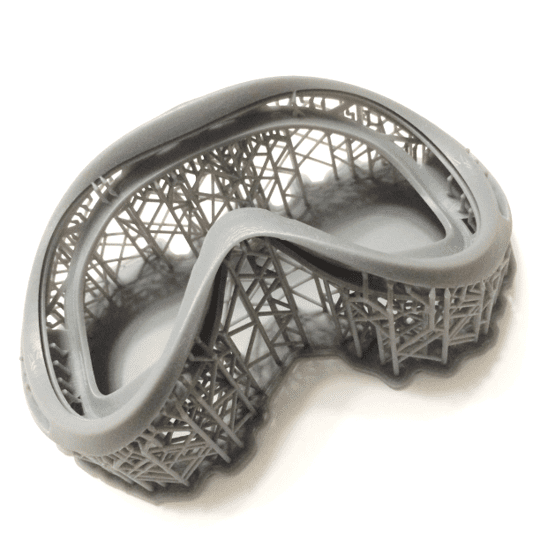
Liqcreate Strong-X is a tough resin known for its strength, high stiffness, and high temperature resistance, making it ideal for heavy-duty applications. It is also low odor and resistant to shrinkage. This resin is particularly well-suited for injection molding, although it is also compatible with 3D printing methods like SLA. The technical specifications for Liqcreate Strong-X, post-curing, include:
- Tensile strength: 91 MPa
- Flexural strength: 135 MPa
- Flexural modulus: 3.25 GPa
- Elongation at break: 8%
- Notched IZOD impact strength: 20 J/m
Work With SyBridge to Choose the Right SLA Tough Resins
SLA tough resins are strong, impact-resistant, and suitable for a wide variety of projects in which a part must withstand stress or strain. These top three brands only scratch the surface when it comes to SLA tough resins. Engineers have many different options, and wading through them all can be overwhelming. An experienced on-demand manufacturing partner can help.
At SyBridge, we want to help our partners push the boundaries of what’s possible and create something truly innovative. Our team of experienced engineers and designers can help product teams make sense of the material selection process and empower them to choose the resin best-suited for their part and their unique requirements. Interested in learning more about SLA tough resins? Contact us today to get started.