Originally published on fastradius.com on January 7, 2021
CNC machining is a traditional manufacturing process that employs cutting tools and drills to systematically remove material from a workpiece to create a finished part. The machine receives toolpaths to cut the piece, typically in G code. The code for the machine can either be manually written, conversationally written at the machine, or output by a post processor from a computer aided manufacturing software (CAM). The process is fast, versatile, repeatable, and highly reliable thanks to the automation that computer numerical controls (CNC) provide.
Since computer software controls the CNC machine and the final outcome of the part, proper CNC machine programming is essential. Poor programming can lead to tolerance issues, poor surface finish, premature tool breakage, and a host of other issues. To ensure consistent results every time, operators and programmers must first grasp the basics.
The Basics of CNC Machine Programming
There are three basic CNC machine programming methods — manual, conversational, and CAM system programming. With manual programming, the operator inputs code manually, which can be time-consuming and somewhat tedious. It also requires intimate knowledge of the programming language. However, manual programming is a valuable foundational skill set to have on hand, and it’s an effective way to make quick modifications to CAM outputs and optimize code.
Conversational or “shop-floor” programming is an increasingly popular method that involves graphic and menu-driven functions. Operators input commands directly into the CNC machine, just like in manual programming, which alleviates potential issues that may arise from poor post processors in CAM. CAM system programming is similar to the conversational method, but more advanced. With a CAM system, the software provides an advanced GUI with tool path strategies to help the operator prepare and generate the program — eliminating the need for any manual programming — and transfer it directly to the CNC machine.
All of these CNC machine programming methods involve G-code and M-code. G-code is the programming language that instructs the CNC machine what to do, facilitating accurate and repeatable parts. M-code controls all of the miscellaneous CNC machine functions, such as spindle rotation start and stop. M-codes are customizable and vary by machine, so operators and programmers must double-check they’re inputting the right functions before they start machining.
Here are four CNC machine programming tips that operators should know:
4 Essential CNC Machine Programming Tips
1. Take time to revisit the basics
The best CNC programmers, operators, and machinists ensure they have mastered the fundamentals before starting any project. For manual and conversational programming, operators should check their math to ensure they’re programming the right specs into the CNC machine.
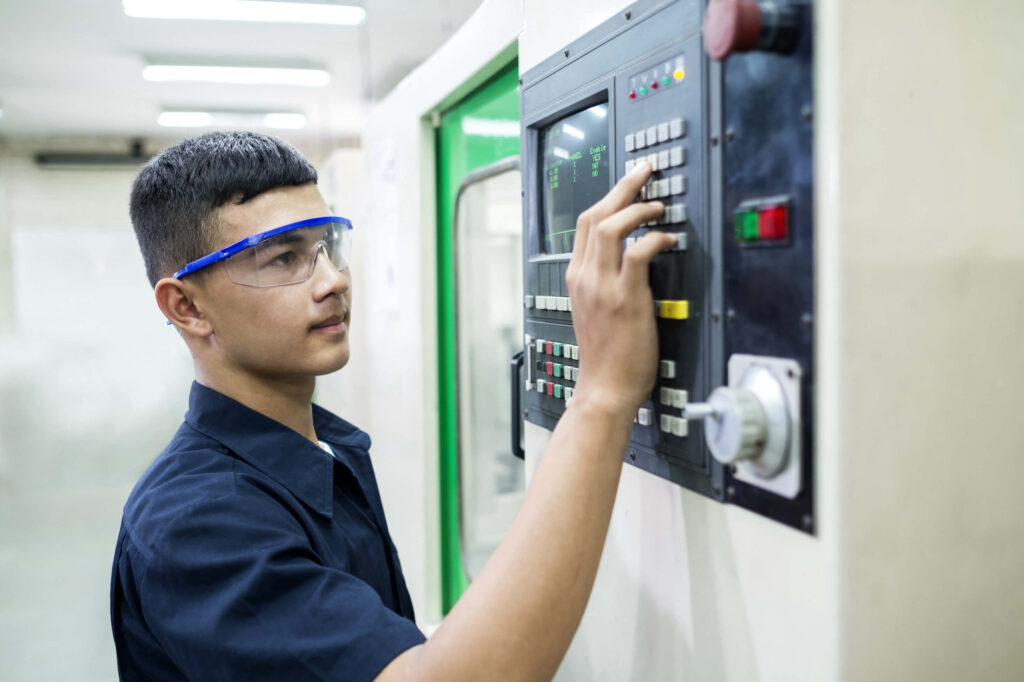
During this preliminary phase, programmers should also remember that CNC software isn’t infallible. For example, most CNC machine programs plot curves and circles as a series of chords instead of a truly curved surface, which can impact any curved lines in the master pattern. A CNC machine program is only as precise as its underlying math, and it never hurts to double check one’s work.
2. Customize CNC machine feed rates
In any high-volume CNC project, operators spend a lot of time dialing in a program to ensure that it runs smoothly, efficiently, and consistently. Once this has been accomplished and the program is locked, operators can “set it and forget it.” However, customizing certain aspects of CNC machine programming can optimize manufacturing.
For example, every single line of code that the CNC machine runs calls out a speed and a feed. If an operator commands a spindle on without making an accompanying speed command, the machine will revert back to its last RPM. The same principle applies to feed rates. During the early stages of any project, operators should be prepared to adjust their feed times based on how well the finished product turns out, and any other relevant data.
3. Understand CNC machine compensation types
Compensation is simply allowing and accounting for unpredictable variations to occur. An operator can input their CNC milling machine programming codes perfectly or calculate which values should yield the perfect part, but they won’t be able to confirm the accuracy and precision of their programming until machining is complete. There are a number of variables that are difficult to account for that may impact results. Tool pressure, for instance, may affect the final product, even when all other initial adjustments and calculations are correct.
Operators should be aware of the most common compensation types and account for them during programming. Compensations can be input manually or programmed using automatic pre-setter tools within the CNC machine. Machining compensation types include tool length compensation, cutter radius compensation, tool wear, and fixture offsets. With each adjustment and compensation, machining becomes more precise.
4. Seize opportunities to simplify CNC machine programming
G-codes are standard for almost all CNC machining programs; however, it can be time-consuming to program operations one by one. Operators can dramatically shorten the programming of hole-machining operations by using canned cycles.
Canned cycles only require one block per hole, regardless of machining style, and once the operator inputs a canned cycle, they can machine additional holes by re-programming the coordinates of the hole only. Codes like G83 save time, reduce errors, and make CNC machine programming easier across the board.
An Expert Manufacturing Partner for Better Results
These essential tips provide an excellent foundation for creating clean and functional CNC-machined parts, but they represent just a fraction of what great manufacturing entails. For manufacturers just getting started in CNC machining, negotiating CNC milling machine programming codes and mastering machine programming best practices can seem overwhelming.
An expert manufacturing partner like SyBridge can ease the burden. Our team of seasoned designers, engineers, manufacturers, and technologists have decades of experience in designing, prototyping, and manufacturing superior CNC-machined parts. With our own fleet of in-house machines, we are expert CNC machine programmers. Our team is prepared to manufacture on-demand CNC-machined parts in a fraction of the time and at a fraction of the cost of other vendors. Contact us today — let’s make new things possible.