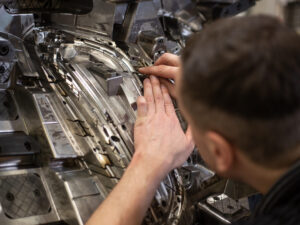
Maintain Uptime and Excellence
Engineering and maintenance services for increased uptime
Scale and flexibility for prompt, reliable and cost-effective support
20 facilities and 1,200+ employees dedicated to your success
Global presence with local execution
Repair and maintenance plans for every service level requirement
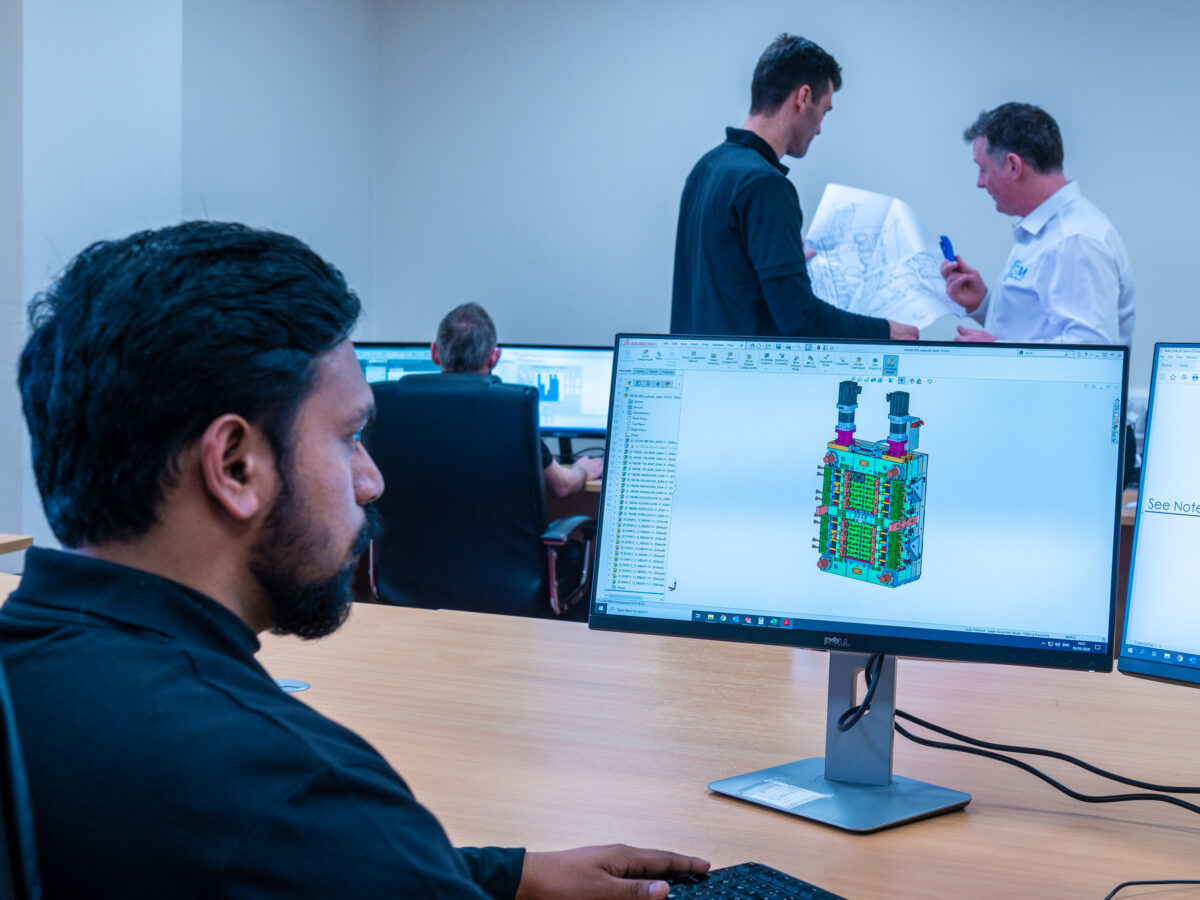
Engineering Changes and Mold Repair
Increase uptime and productivity with our comprehensive mold repair and refurbishment services. With industry-leading capabilities and locations across the US, Canada and Mexico, our quick and affordable engineering change and mold repair services can help you maximize your production efficiency.
Our repair and refurbishment services include:
- Root Cause Analysis of Mold Failures
- Repair or Replacement of Mold Components
- Reverse Engineering of Existing Tools
Landing Services
To help our customers manufacture and move parts around the world, we offer an array of cost-effective landing services that include:
- Global Logistics and Supply Chain Support
- Offshore Mold Delivery
- Texture Program Management
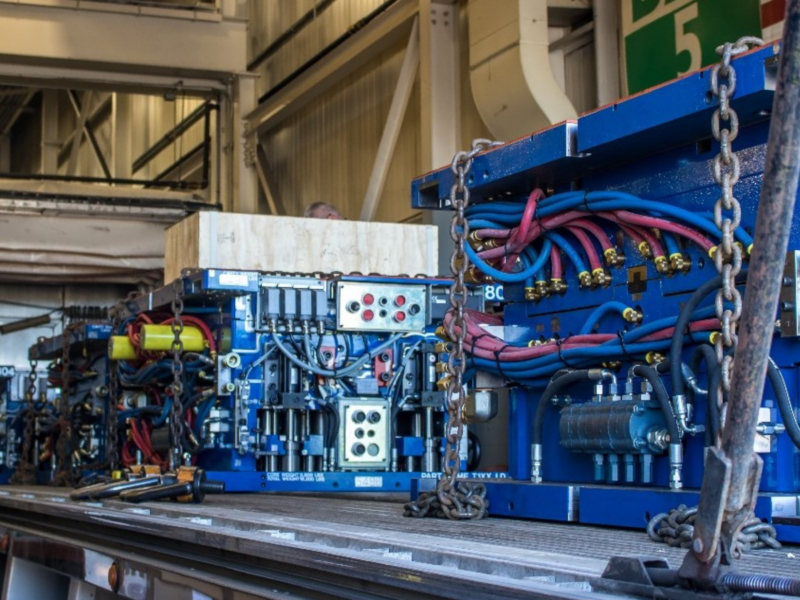
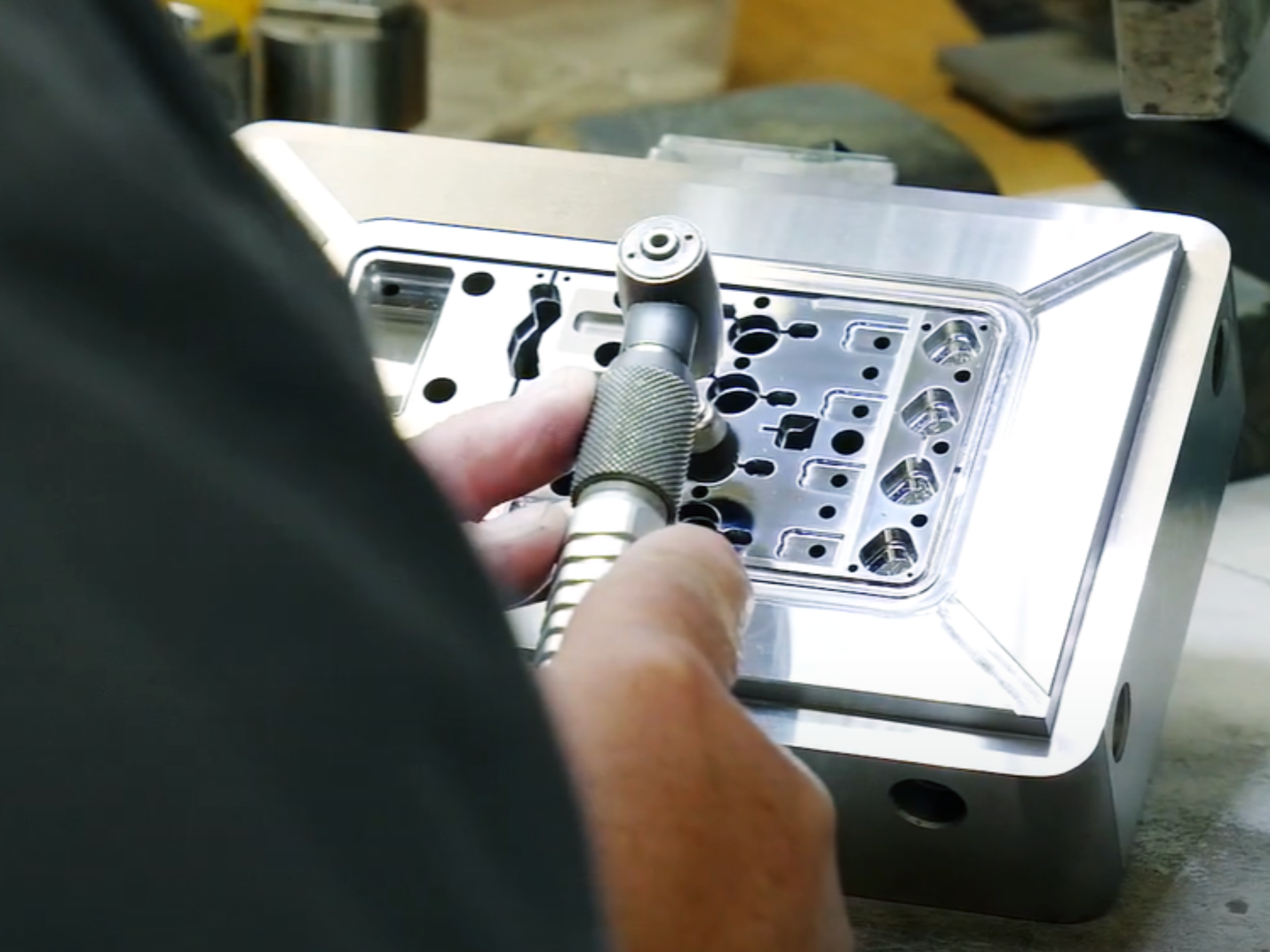
Preventative Maintenance Plans
With proactive measures, you can increase equipment lifespan, reduce downtime and save money by avoiding costly repairs and stoppages. Choose from two comprehensive pre-defined service plans or specify your own support requirements for a custom plan that meets your specific needs.
Our preventative maintenance services include:
- Silver, Gold and Custom Preventative Maintenance Plans
- Rapid Response Teams for On-Site Support
- Quick Replacement Part Delivery
Preventative Maintenance Plans Tailored to Your Needs
Looking to reduce downtime, prevent avoidable repairs and save on overall costs? Explore our comprehensive Preventative Maintenance Plans today!
Silver Plan
- Comprehensive incoming inspection, including documenting cycle counter and manifold temperatures
- Water line blow-out
- Disassembly, cleaning, lubrication and re-assembly (excluding hot runners)
- Functional testing and outgoing inspection
Gold Plan
- Comprehensive incoming inspection, including documenting cycle counter and manifold temperatures
- Water line blow-out
- Logging and documentation of GPM per water circuit
- Full inspection of hot runner system, including clamp plate removal, plumbing and wiring
- Full heat test
- Replacement of worn items, such as bushings and pins
- Functional testing and outgoing inspection
Customized Plan
- Includes choice of Silver or Gold plan plus re-spotting
- Customer-specific requirements
Pricing for custom plans varies based on customer requirements. Holiday and weekend options carry a premium. Volume discount on services within a calendar year are available based on spend level. Transportation can be arranged through SyBridge Technologies. Additional charges (round trip) apply. Invoiced monthly via blanket PO under normal payment terms.