Originally published on fastradius.com on September 21, 2021
Computer Numerical Control (CNC) machining is a subtractive manufacturing process that enables manufacturers to accurately and cost-effectively create high-precision parts. CNC machining removes excess raw material from workpieces with cutting tools to create a precise finished product from materials like plastic, metal, and composites.
These days, product teams have lots of options when it comes to multi-axis machining, from 3-axis to 5-axis to even 9-axis machining. What’s the difference between each type? In this article, we’ll break down the key similarities and differences between two popular types of CNC machining (3-axis vs. 5-axis) — and explain when it might make sense to use one over the other.
3-Axis Machining
After the operator enters milling instructions into a computer, the 3-axis CNC machine will automatically complete the task by using a tool to cut along three axes — X, Y, and Z, or left-to-right, front-to-back, and up-and-down. Both CNC milling and CNC turning fall under the umbrella of 3-axis machining. However, they function slightly differently.
When using a 3-axis CNC milling machine, the material block remains fixed in a vice or on a machine bed. Rotating drills or cutting tools are connected to a spindle and move along the X, Y, and Z axes, removing shavings to accurately form the final component. 3-axis CNC milling machines are excellent for producing most geometries and simple parts.
By contrast, in the CNC turning process, the workpiece is attached to a rotating spindle, and a lathe shapes the component. As the spindle holding the workpiece rotates, a center drill or cutting tool traces the component’s outer and inner perimeters or creates holes along the center axis. Compared to CNC milling machines, CNC lathe turning machines produce parts faster and offer cheaper per-unit costs, which is advantageous for high-volume production runs.
Since a 3-axis CNC machine can only cut along three axes, it may struggle with non-conventional shapes or designs with deep, narrow cavities that are difficult to reach. When processing parts with complex geometries, operators may have to manually reposition the workpiece, which can slow down the processing speed, raise labor and machining expenses, and result in a less-than-perfect finished product.
5-Axis Machining
5-axis machines rely on a tool that moves in five different directions — X, Y, and Z, as well as A and B, around which the tool rotates. Using a 5-axis CNC machine lets operators approach a part from all directions in a single operation, eliminating the need to manually reposition the workpiece between operations. 5-axis CNC machining saves time and is ideal for creating complex and precise parts like those found in the medical, oil and gas, and aerospace industries. There are a few different kinds of 5-axis machines that product teams should be aware of, including indexed 5-axis CNC machines, continuous 5-axis CNC machines, and mill-turning CNC centers.
Like 3-axis CNC milling, the cutting tool only moves along three axes and doesn’t maintain continuous contact with the workpiece in indexed 5-axis CNC machining. However, the machining table and tool head can automatically swivel in two directions between operations. Indexed 5-axis machining is great for manufacturing housings, jigs and fixtures. It falls somewhere between 3-axis CNC milling and continuous 5-axis CNC machining in terms of speed, precision, and the ability to handle complex geometries.
In continuous 5-axis CNC machining, the cutting tool and the workpiece can rotate and move simultaneously during operation, saving time and allowing operators to manufacture intricate geometries with organic surfaces. Continuous 5-axis CNC machining offers improved surface finish, speed, and dimensional stability, but it has the highest cost-per-part.
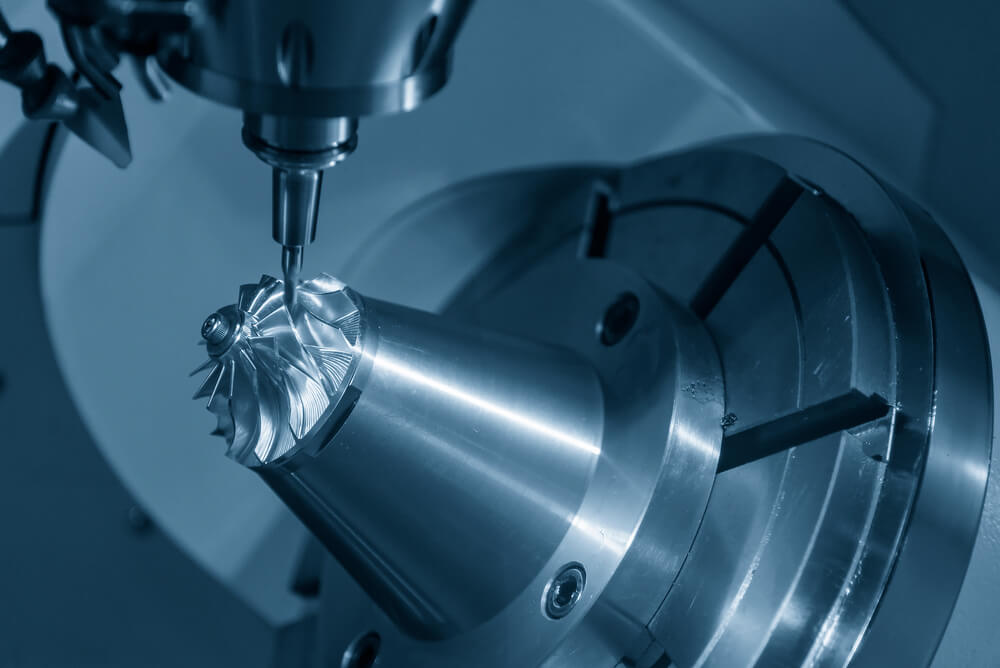
Turning mill CNC centers are practically identical to CNC turning machines, with one exception — they’re equipped with CNC milling equipment. The workpiece is attached to a spindle that can either rotate or remain stationary while cutting tools remove material from it. By combining the elements of CNC lathe machines with milling tools, mill-turning CNC centers offer high levels of accuracy and geometric versatility, making them great for creating parts with loose rotational symmetries, such as camshafts or centrifugal compressors.
Not only do these types of 5-axis CNC milling machines offer greater accuracy when machining deeper parts and hardened materials, but they also offer higher yields and faster machining speeds. However, 5-axis machining is more expensive due to the specialized equipment necessary and the need for expert workers.
3-Axis Machining vs. 5-Axis Machining
The main difference between 3-axis and 5-axis milling machines is that the workpiece can be worked on from three axes with the former and five axes with the latter. Both are highly versatile, automated, and replicable production processes that will enable you to quickly and cost-effectively create accurate components. However, you may opt to use one over the other for a variety of reasons.
If you’re on a budget or only need to cut a flat surface, 3-axis machines might be the way to go. In addition to being more affordable than those with five axes, 3-axis machines are simpler to program, so you won’t have to incur the cost of working with expensive expert programmers and operators. Plus, prep time is shorter with 3-axis machining.
If you need to produce a deeper part or one with complex geometry, you’ll probably want to use 5-axis machining. Using 5-axis machines lets you machine the workpiece from all sides — no manual rotation required. With 5-axis machining, you’ll have higher yields, greater accuracy, and increased freedom of movement, as well as the ability to manufacture larger parts faster.
Work With SyBridge
Still on the fence about using a 5-axis CNC machine vs. a 3-axis machine? SyBridge can help. Our team of experts can talk you through your CNC machining options and help you choose the process that’s best for your project. As a trusted CNC machining partner, SyBridge also offers high-quality CNC machining capabilities with router-, lathe-, drill-, and mill-based CNC machining equipment. Contact us today to get started.